
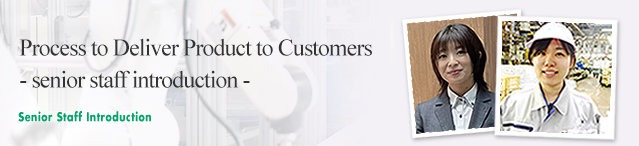
- quality assurance
Quality assurance is a never-ending task
First Quality Assurance Section, Quality Assurance Department, Production Headquarters
Yamaguchi University Graduate School of Science and Engineering Department of Materials Science
Joined in 2017

- Please tell us about your current work
- In the 1st Quality Assurance Section, I am in charge of quality assurance work from the development stage to the beginning of mass production. Quality assurance may have an image of responding to complaints, but that is only a small part. This is a department that examines whether it is okay to deliver products, including prototypes and mass-produced products, to customers.
Based on the characteristics of the product shape and equipment of the new product, what kind of problems are likely to occur when it goes into mass production, and based on past troubles, we will check from a wide perspective whether there are any pitfalls in the process of each department.
In addition, since Kurashiki Kako Kako products use metal products purchased from subcontractors, we sometimes visit overseas manufacturers directly to check the manufacturing process and examine whether there are any concerns about mass production.
There is no goal in quality assurance, and it is a very difficult job, but I feel that my work is very rewarding because my work is directly linked to the quality of the product.
- Please tell us about the attractiveness of the company
- Kurashiki Kako Kako has a two-division structure, the Automotive Parts Division and the Industrial Equipment Division, and has entered a wide range of fields. In addition to steadily increasing sales every year, there are prospects for further market expansion, and I feel that this is a company that can continue to grow.
As for the corporate culture, I feel that there are many people with gentle and kind personalities. As a result, even though I am new to the company, I am able to actively speak out, and I have been entrusted with important tasks from a young age.
I feel that I have many opportunities to improve my skills because I am proactive in education and can participate in seminars that I am interested in.
- Please tell us about the most “heartbreaking job” you have ever had.
- I was most impressed by the resolution of a very difficult problem that occurred in a new part.
As the person in charge of the Quality Assurance Department, I led the investigation of the cause and the planning of countermeasures while collaborating with other departments for defects that occurred before mass production. Various hypotheses were formulated and verified, and the effectiveness of countermeasures was repeatedly confirmed. It took a very long time and man-hours, but we were able to identify the cause and completely prevent the failure.
Since the measures were implemented with the cooperation of many stakeholders, including internal suppliers and external suppliers, I felt a great sense of accomplishment when I was able to confirm their effectiveness.
I was very happy when people outside the company and on-site people told me, "You did a great job!"
However, the quality assurance work does not end here, and the most important job is to prevent similar problems from occurring in the next new parts. Based on this experience, we aim to grow further and become a stronger force in terms of how we can prevent problems in the future.
- Please tell us your motto!
